Quick and Reliable Packaging Maker Repair Work Provider to Lessen Downtime
In the competitive landscape of production, the efficiency of packaging procedures hinges on the dependability of equipment. Quick and trustworthy repair services are crucial in minimizing downtime, which can lead to significant monetary losses and functional troubles.
Significance of Timely Fixes
Prompt repairs of packaging devices are vital for keeping functional performance and decreasing downtime. In the busy setting of manufacturing and product packaging, also small breakdowns can bring about substantial hold-ups and performance losses. Resolving problems immediately makes sure that devices operate at their optimal ability, therefore guarding the circulation of operations.
Furthermore, regular and prompt maintenance can prevent the rise of small problems into major break downs, which frequently sustain higher repair service expenses and longer downtimes. A proactive approach to equipment repair service not only maintains the stability of the equipment yet likewise enhances the total dependability of the assembly line.
In addition, timely repairs add to the longevity of product packaging machinery. Equipments that are serviced without delay are less likely to deal with too much deterioration, permitting services to maximize their investments. This is particularly vital in industries where high-speed product packaging is vital, as the need for constant performance is critical.
Advantages of Reliable Provider
Trustworthy service companies play an essential role in ensuring the smooth procedure of product packaging machines. Their know-how not only enhances the efficiency of fixings however likewise contributes considerably to the longevity of equipment. Trustworthy provider are furnished with the technological knowledge and experience necessary to identify issues precisely and carry out effective remedies promptly. This reduces the danger of recurring problems and makes certain that equipments operate at optimal performance degrees.
Furthermore, a credible company uses thorough assistance, including training and assistance for personnel on machine procedure and upkeep best methods. This not only equips employees yet likewise grows a culture of safety and security and performance within the company. In general, the advantages of engaging trusted company extend past instant repair work, favorably impacting the entire operational workflow of packaging procedures.
Usual Packaging Device Problems
In the world of packaging procedures, various problems can endanger the performance and functionality of equipments. One prevalent trouble is mechanical failing, commonly stemming from deterioration or inadequate maintenance. Elements such as equipments, belts, and electric motors may stop working, resulting in failures that stop production. An additional common problem is misalignment, which can trigger jams and irregular product packaging, affecting product quality and throughput.
Electrical troubles can additionally interrupt packaging procedures. Damaged electrical wiring or malfunctioning sensing units might lead to unpredictable equipment habits, creating hold-ups and raised functional prices. you can find out more Additionally, software application problems can hinder the maker's programming, leading to functional ineffectiveness.
Inconsistent product circulation is an additional essential problem. This can develop from variations in item dimension, weight, or form, which may influence the maker's capacity to handle products precisely. Not enough training of operators can intensify these troubles, as untrained personnel may not identify early indications of malfunction or might abuse the equipment.
Dealing with these usual packaging device problems immediately is important to keeping productivity and making sure a smooth procedure. Normal examinations and proactive maintenance can considerably minimize these worries, promoting a trustworthy packaging atmosphere.
Tips for Lessening Downtime
To reduce downtime in product packaging operations, applying a positive upkeep technique is important. Routinely arranged maintenance checks can identify possible problems prior to they intensify, making sure equipments run effectively. Establishing a regimen that includes lubrication, calibration, and inspection of critical parts can dramatically reduce the frequency of unanticipated failures.
Training personnel to operate machinery correctly and recognize early indication of breakdown can likewise play an important role. Encouraging drivers with the knowledge to do fundamental troubleshooting can prevent small issues from creating significant hold-ups. Additionally, maintaining an efficient stock of vital spare parts can quicken fixings, as waiting on parts can cause extensive downtime.
Furthermore, documenting device efficiency and maintenance activities can assist identify patterns and frequent issues, enabling targeted interventions. Incorporating sophisticated tracking innovations can supply real-time information, allowing predictive upkeep and decreasing the danger of abrupt failings.
Last but not least, promoting open interaction between operators and maintenance teams makes certain that any kind of irregularities are quickly reported and resolved. By taking these aggressive actions, companies can improve operational effectiveness and significantly minimize downtime in packaging processes.
Choosing the Right Repair Work Service
Selecting the proper repair work service for packaging devices is an essential choice that can significantly affect functional efficiency. An appropriate company guarantees that your equipment is fixed swiftly, successfully, and to the greatest standards. Begin by reviewing the copyright's experience with your details sort of product packaging equipment. A specialist acquainted with your equipment can detect concerns more properly and implement remedies more quickly.
Following, take into consideration the service provider's online reputation. Looking for comments from blog here other businesses within your industry can offer insights into dependability and top quality. Certifications and partnerships with acknowledged devices makers can additionally show a dedication to excellence.
In addition, analyze their response time and availability. A service supplier that can provide prompt assistance lessens downtime and maintains production flow steady. It's also crucial to ask regarding warranty and service assurances, which can mirror the confidence the company has in their work.
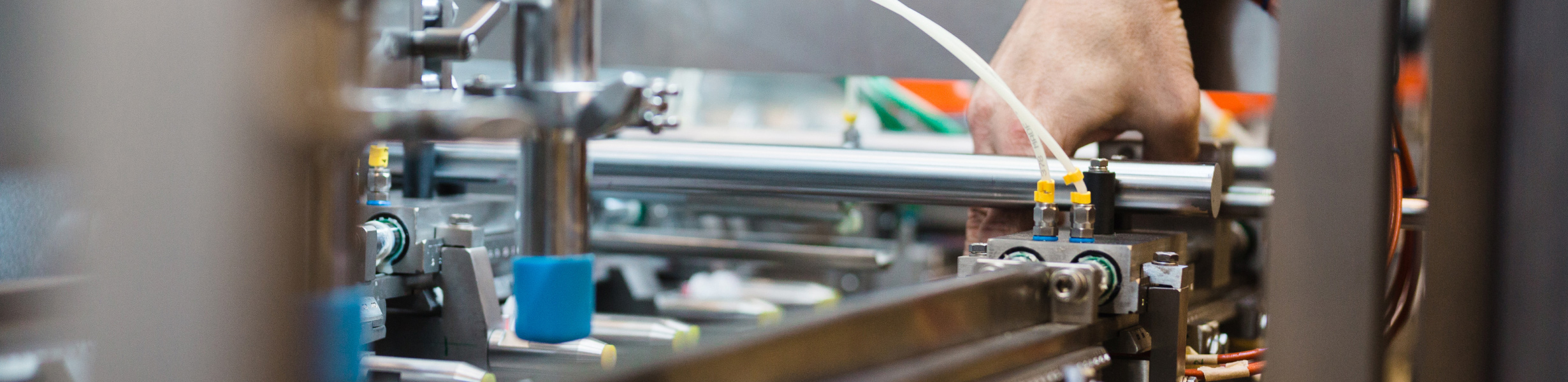
Conclusion
In verdict, the relevance of fast and trustworthy product packaging device repair solutions can not be overemphasized, as they play a vital role in lessening downtime and ensuring operational efficiency. Applying proactive upkeep practices and investing in staff training more enhances the long life of product packaging equipment.
Prompt repair work of packaging machines are important for maintaining operational effectiveness and decreasing downtime.In addition, prompt you could look here repair services contribute to the long life of packaging equipment. Generally, the benefits of involving trustworthy service suppliers extend beyond immediate fixings, favorably influencing the entire operational operations of packaging processes.
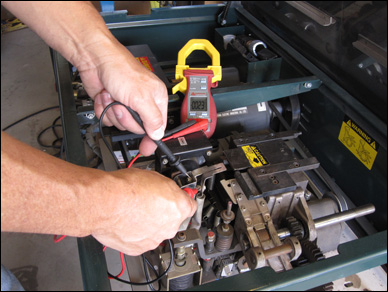